Le piastre d’appoggio
Dal principio
Iniziamo con qualche curiosità prima di parlare delle piastre. A partire dalla fine degli anni ’20 e poi negli anni ’30 le materie plastiche sono state le protagoniste di innumerevoli ricerche e approfonditi studi tali da permetterne un impiego sempre più crescente in qualsiasi settore di applicazione. Non esclusivamente a livello domestico, ma principalmente a livello industriale. Si tratta infatti di materiali aventi ottime proprietà chimiche e meccaniche, eguagliabili se non superiori alle caratteristiche di altri materiali utilizzati da secoli, ma che hanno il vantaggio di abbattere facilmente i costi ed essere durevoli.
Ma quelle che noi tutti chiamiamo comunemente plastiche, come si definiscono sotto un profilo chimico e fisico? Si tratta di materiali che contengono come costituenti fondamentali uno o più polimeri di alto peso molecolare. Più facilmente delle sostanze costituite da molecole di grandi dimensioni, dette macromolecole, formatesi tramite l’unione secondo legami chimici stabili di unità dette monomeri o polimeri di base. Si ottengono dal processo di raffinazione del petrolio, il quale origina nafte pesanti, che lavorate mediante cracking per via catalitica o termica, producono polimeri di base come l’elitene, il propilene, il metano, l’etilbenzolo, e altri. Attraverso successive lavorazioni e processi chimici (polimerizzazione) si ottengono i prodotti finiti che vengono commercializzati.
In base alla struttura molecolare, il materiale manifesta particolari proprietà chimiche e meccaniche. Le principali categorie in cui si suddividono sono tre:
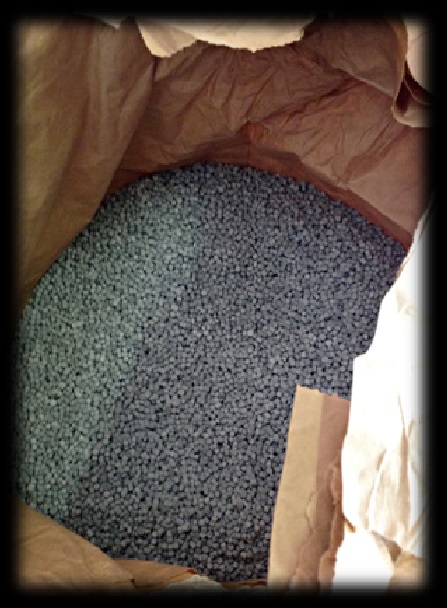
Globalmente tutti questi prodotti conservano delle proprietà comuni vantaggiose:
leggerezza / inerzia chimica / basso coefficiente di attrito / bassa conducibilità, sia termica che elettrica / buone proprietà ottiche / costo relativamente modesto, grazie ai processi di formazione poco dispendiosi, all’eliminazione dei processi di finitura e rivestimenti protettivi, e alla possibilità di riciclo.
Focus On
Limitando considerevolmente l’ambito di impiego, nello specifico nel nostro settore i polimeri maggiormente adoperati sono il POLIETILENE e il POLIPROPILENE.
Il POLIETILENE è certamente il materiale più diffuso e costituente il 40% della produzione mondiale di materie plastiche. Attraverso due diversi processi si ottengono il polietilene a bassa densità, impiegato per la produzione di imballaggi, film, contenitori e come isolante elettrico. L’altro è il polietilene ad alta densità che grazie all’inerzia chimica può costituire serbatoi, recipienti e tubazioni.
Risulta per noi più interessante trattare un altro importantissimo polimero termoplastico, il POLIPROPILENE, elemento centrale nella produzione di spessori e distanziatori.
Ottenuto per poliaddizione dal gas propilene, può essere omopolimero, copolimero a blocchi o random.
A livello chimico strutturale si può individuare un ulteriore diversificazione: se i gruppi sostituenti, n questo caso i gruppi metilici, si collocano tutti dalla stessa parte della catena polimerica, si ha isomeria posizionale che provoca una struttura isotattica; diversamente se si posizionano casualmente sui due lati della catena, la struttura è atattica.
Sotto un profilo commerciale il più utilizzato è il polipropilene isotattico: infatti presentando un’elevata cristallinità, il materiale è piuttosto rigido.
Ciò determina proprietà meccaniche estremamente vantaggiose, un elevato carico di rottura, una densità relativamente bassa, un ridotto coefficiente percentuale di assorbimento d’acqua, temperatura di fusione di 165°C, buone proprietà coibentanti avendo conducibilità termica k di circa 0.1-0.22 W/(m K).
Il Sistema Produttivo
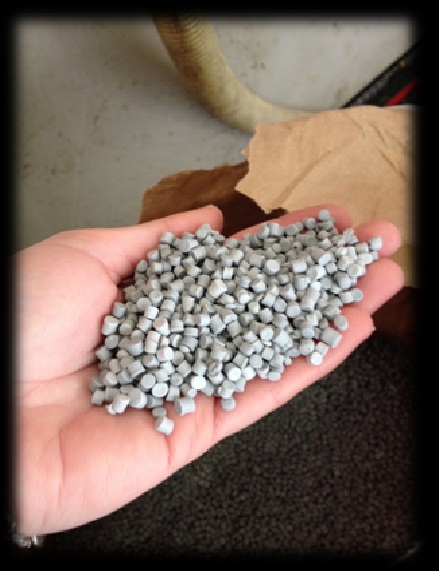
I sistemi di appoggio, ovvero le piastre utilizzate in vari settori dell’ingegneria civile ed edile, si producono mediante una particolare tecnologia di formatura: lo STAMPAGGIO AD INIEZIONE.
Il materiale granulo viene caricato attraverso la tramoggia nella pressa a iniezione, ovvero nella zona di alimentazione della vite rotante, posizionata all’interno di un condotto cilindrico in cui sono posizionate a intervalli regolari delle resistenze. Mediante la rotazione della vite, si manifesta un aumento di temperatura che porta il materiale allo stato fluido, dopodichè il materiale plastificato viene spinto nella camera di accumulo. Successivamente la vite punzonante trasla verso l’ugello, spingendo il materiale nello stampo.
In questa fase di compattazione è necessario che il sistema sia mantenuto in pressione, per cui viene iniettata una quantità aggiuntiva di materiale per riempire interamente lo stampo compensando in tal modo la variazione di volume e l’eventuale ritiro del materiale.
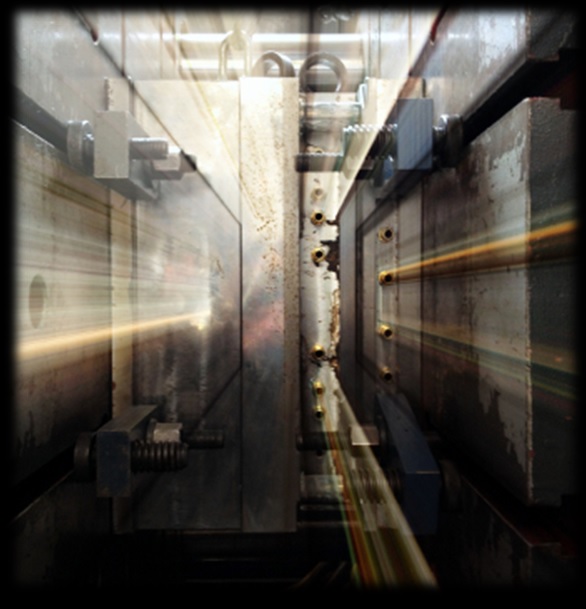
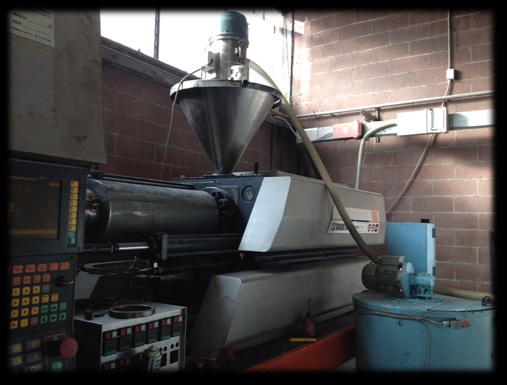
Il materiale permane dunque nello stampo per il tempo necessario alla perfetta solidificazione del materiale, catalizzata da un raffreddamento controllato mediante getti di acqua fredda. Si avvia dunque la fase finale di espulsione del prodotto: lo stampo si apre e gli iniettori presenti sulla piastra mobile spingono l’articolo fuori dallo stampo.
Dal momento che tale processo permette lo stampaggio a due o più figure, si ottengono con un solo ciclo più articoli, che al momento dell’apertura dello stampo sono uniti dalla materozza, la quale non è altro che il materiale solidificato nei canali di iniezione.
Una volta rimosso lo scarto, si ha tra le mani i singoli articoli pronti per essere commercializzati.
Gli spessori rappresentano un’entità fondamentale nella fase di montaggio delle componenti strutturali prefabbricate, quali pannelli di tamponamento, travi, pilastri.Va innanzitutto chiarito che tali dispositivi non assolvono alla funzione di sostegno delle strutture prefabbricate, ma rispondono all’esigenza di ridistribuire le pressioni di contatto su di un’area sufficientemente ampia.
Le piastre d’appoggio
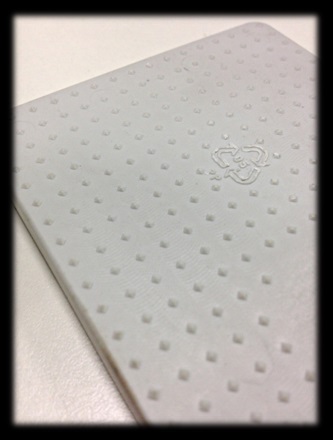
Occhio al dettaglio
In un mercato che offre una vasta concorrenza, noi abbiamo voluto distinguerci investendo su qualità e garanzia. Chiunque stringa tra le mani una piastra di nostra produzione non può non avvertire la precisione che la contraddistingue.
La struttura è perfettamente regolare, senza incurvamenti ne disomogeneità. Entrambe le superfici inferiore e superiore sono arricchite dalla presenza di punti di ancoraggio piramidali equidistanti, che assicurano il corretto assestamento dei carichi sovrapposti e ostacolano un errato scorrimento superficiale.
Inoltre, consapevoli della necessità di poter contare su una fornitura valida ed esauriente, abbiamo sottoposto i prodotti a test di laboratorio presso enti preposti ottenendo un’importante certificazione attestante la resistenza senza rottura a una compressione da 40T fino a 100T.
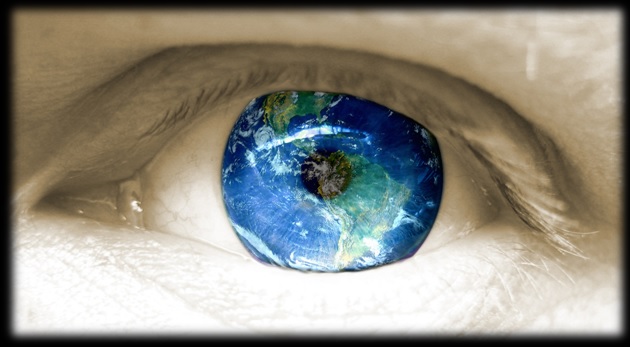